SEMINAR ABSTRACT:
Wavelet methods in Computational Fluid Dynamics is a relatively young area of research. Despite their short three decade-long existence, a substantial number of wavelet techniques have been developed for numerical simulations of compressible and incompressible Euler and Navier--Stokes equations for both inert and reactive flows. What distinguishes wavelet methods from traditional approaches is their ability to unambiguously identify and isolate localized dynamically dominant flow structures such as shocks, flame fronts or vortices and to track these structures on adaptive computational meshes. This lecture will provide a general overview of wavelet methods for solution of partial differential equations and describe different numerical wavelet-based approaches for solving the Navier—Stokes and Euler equations in adaptive wavelet bases as well as provide the background how to use wavelet-based methods to model compressible and incompressible flows in complex geometries. Recent developments such as wavelet methods with mesh and anisotropy adaptation and characteristic-based volume penalization method, capable to impose arbitrary boundary conditions on stationary and moving boundaries, will be also discussed. Perspectives on using wavelet methods for modeling and computing industrially relevant flows will be also given.
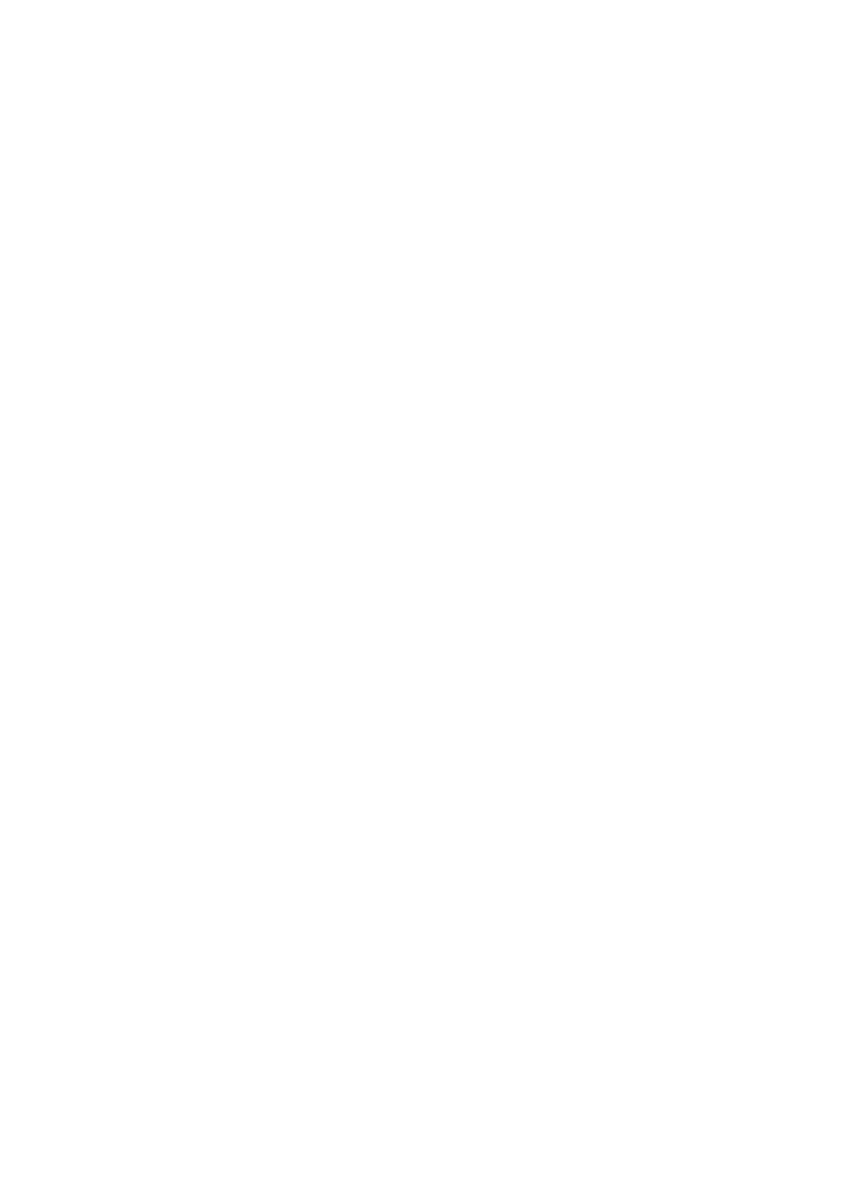
Prof. Oleg Vasilyev received his MSc degree in Applied Mathematics and Physics from Moscow Institute of Physics and Technology in 1991, the MSc and PhD degrees in Mechanical Engineering from the University of Notre Dame, in 1994 and 1996, respectively, and Doctor of Sciences degree in Computational Mathematics in 2021 from Keldysh Institute of Applied Mathematics of Russian Academy of Sciences. Prior to rejoining Skoltech in 2023, Prof. Vasilyev has worked as a leading research scientist at the Keldysh Institute of Applied Mathematics of Russian Academy of Sciences, a consultant for Huawei Russian Research Institute, a Professor at the Center for Design, Manufacturing and Materials of the Skolkovo Institute of Science and Technology, a Professor in the Department of Mechanical Engineering at the University of Colorado, an Assistant Professor in the Department of Mechanical and Aerospace Engineering at the University of Missouri – Columbia, and a Research Fellow at the Center for Turbulence Research, Stanford University.
Prof. Vasilyev conducts research in the general area of theoretical and computational fluid mechanics with the emphasis on the creation of novel adaptive approaches for modeling and simulation of complex multi-scale phenomena, development of low order “physics-capturing” models and robust computational methodologies with tight integration of the numerics and physics-based modeling, and applications of these novel approaches to challenging multi-scale/multi-physics fluid problems of engineering and scientific interest. Prof. Vasilyev is the author and co-author of more than 100 peer-reviewed journal and conference publications. He has given more than 200 lectures at conferences at universities around the world. For his research accomplishments, Prof. Vasilyev has been recognized with several awards and honors including a Fredric William Basel Research Award from Alexander Von Humboldt Foundation and has been elected a Fellow of the American Physical Society and a Fellow of the American Society of Mechanical Engineers.